What measures do fire pump suppliers take to ensure safety and compliance in their manufacturing processes?
Mar 01, 2024
Share:
Fire pump suppliers take several measures to ensure safety and compliance in their manufacturing processes. These measures are essential to produce reliable products that meet regulatory requirements and contribute to the overall safety of fire protection systems. Here are some key steps they take:
1. **Adherence to Regulations and Standards**: Fire pump suppliers closely follow relevant regulations and industry standards governing the design, manufacturing, and installation of fire pumps. This includes standards established by organizations such as the NFPA, UL, and ISO. By adhering to these standards, suppliers ensure that their products meet minimum safety requirements and performance criteria.
2. **Risk Assessment and Hazard Analysis**: Suppliers conduct thorough risk assessments and hazard analyses to identify potential safety hazards associated with their manufacturing processes. This proactive approach allows them to implement appropriate safety measures and controls to mitigate risks and prevent accidents.
3. **Employee Training and Education**: Suppliers provide comprehensive training and education programs for their employees to ensure they understand safety protocols, best practices, and regulatory requirements. Training may cover topics such as equipment handling, chemical safety, emergency procedures, and compliance with relevant standards.
4. **Safety Equipment and Personal Protective Gear**: Suppliers equip their manufacturing facilities with appropriate safety equipment, such as fire extinguishers, emergency showers, eye wash stations, and ventilation systems. Additionally, they provide employees with personal protective gear, including safety glasses, gloves, helmets, and protective clothing, to minimize the risk of injury or exposure to hazards.
5. **Quality Control and Assurance**: Stringent quality control and assurance measures are implemented throughout the manufacturing process to identify and address any potential safety or compliance issues. This includes inspection of raw materials, in-process monitoring, and final product testing to ensure that fire pumps meet specified quality standards and performance criteria.
6. **Documented Procedures and Records**: Suppliers maintain documented procedures and records of their manufacturing processes, including quality control measures, test results, and compliance documentation. These records provide evidence of compliance with regulatory requirements and facilitate traceability and accountability.
7. **Supplier Audits and Inspections**: Suppliers may undergo regular audits and inspections by regulatory agencies, independent third-party organizations, or customers to verify compliance with safety standards and regulations. These audits help identify areas for improvement and ensure ongoing adherence to safety protocols.
8. **Continuous Improvement**: Suppliers continuously evaluate and improve their manufacturing processes to enhance safety, efficiency, and product quality. This may involve implementing new technologies, adopting best practices, and incorporating feedback from customers and stakeholders.
By implementing these measures, fire pump suppliers prioritize safety and compliance in their manufacturing processes, ultimately delivering products that meet the highest standards of quality and reliability.
1. **Adherence to Regulations and Standards**: Fire pump suppliers closely follow relevant regulations and industry standards governing the design, manufacturing, and installation of fire pumps. This includes standards established by organizations such as the NFPA, UL, and ISO. By adhering to these standards, suppliers ensure that their products meet minimum safety requirements and performance criteria.
2. **Risk Assessment and Hazard Analysis**: Suppliers conduct thorough risk assessments and hazard analyses to identify potential safety hazards associated with their manufacturing processes. This proactive approach allows them to implement appropriate safety measures and controls to mitigate risks and prevent accidents.
3. **Employee Training and Education**: Suppliers provide comprehensive training and education programs for their employees to ensure they understand safety protocols, best practices, and regulatory requirements. Training may cover topics such as equipment handling, chemical safety, emergency procedures, and compliance with relevant standards.
4. **Safety Equipment and Personal Protective Gear**: Suppliers equip their manufacturing facilities with appropriate safety equipment, such as fire extinguishers, emergency showers, eye wash stations, and ventilation systems. Additionally, they provide employees with personal protective gear, including safety glasses, gloves, helmets, and protective clothing, to minimize the risk of injury or exposure to hazards.
5. **Quality Control and Assurance**: Stringent quality control and assurance measures are implemented throughout the manufacturing process to identify and address any potential safety or compliance issues. This includes inspection of raw materials, in-process monitoring, and final product testing to ensure that fire pumps meet specified quality standards and performance criteria.
6. **Documented Procedures and Records**: Suppliers maintain documented procedures and records of their manufacturing processes, including quality control measures, test results, and compliance documentation. These records provide evidence of compliance with regulatory requirements and facilitate traceability and accountability.
7. **Supplier Audits and Inspections**: Suppliers may undergo regular audits and inspections by regulatory agencies, independent third-party organizations, or customers to verify compliance with safety standards and regulations. These audits help identify areas for improvement and ensure ongoing adherence to safety protocols.
8. **Continuous Improvement**: Suppliers continuously evaluate and improve their manufacturing processes to enhance safety, efficiency, and product quality. This may involve implementing new technologies, adopting best practices, and incorporating feedback from customers and stakeholders.
By implementing these measures, fire pump suppliers prioritize safety and compliance in their manufacturing processes, ultimately delivering products that meet the highest standards of quality and reliability.
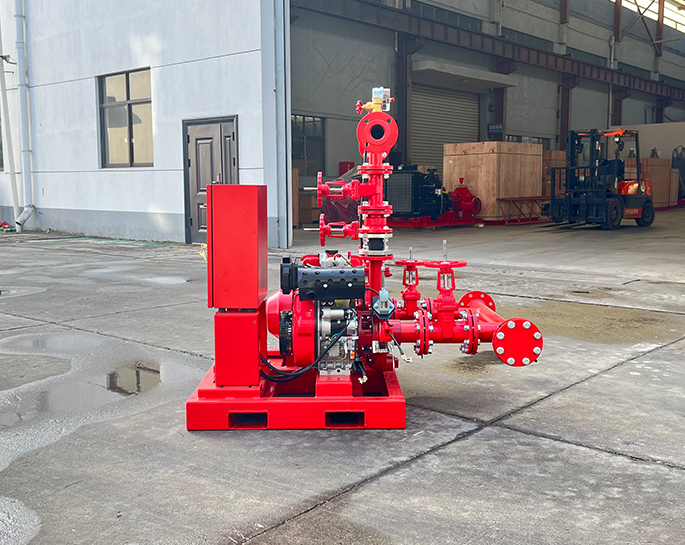