What measures are taken to prevent corrosion in fire pump controllers or electronic components?
Jan 09, 2024
Share:
Preventing corrosion in fire pump controllers and electronic components is crucial for ensuring the reliable operation of the system. Here are several measures commonly taken to mitigate the risk of corrosion:
1. **Enclosures and Sealing:**
- **Weatherproof Enclosures:** Fire pump controllers are often housed in weatherproof enclosures that protect the electronic components from environmental elements such as rain, snow, and humidity.
- **IP Ratings:** Enclosures are designed with specific Ingress Protection (IP) ratings to indicate their resistance to moisture and dust. Higher IP ratings provide better protection against environmental factors.
2. **Corrosion-Resistant Materials:**
- **Component Selection:** Choosing electronic components and materials that are corrosion-resistant is essential. This includes using corrosion-resistant metals, coatings, and materials for the construction of the controllers.
3. **Sealed Connectors and Joints:**
- **Sealed Connectors:** Electrical connectors should be designed to be water-resistant or waterproof to prevent moisture ingress.
- **Joints and Seams:** Proper sealing of joints and seams in the enclosure helps prevent water infiltration. Gaskets, seals, and adhesives may be used for this purpose.
4. **Coatings and Finishes:**
- **Protective Coatings:** Applying protective coatings to electronic components and surfaces can help prevent corrosion. This may include coatings with corrosion-resistant properties, such as epoxy or other specialized coatings.
- **Powder Coating:** Some controllers may have a powder-coated finish, which provides an additional layer of protection against corrosion.
5. **Ventilation and Air Circulation:**
- **Proper Ventilation:** Adequate ventilation is essential to prevent condensation inside the enclosure. Proper airflow helps maintain a more stable internal environment, reducing the risk of moisture-related corrosion.
6. **Environmental Monitoring:**
- **Humidity Sensors:** Installing humidity sensors within the enclosure allows for monitoring and controlling the humidity levels. This information can trigger alarms or actions to mitigate excessive moisture.
7. **Regular Inspections and Maintenance:**
- **Scheduled Inspections:** Regular inspections of fire pump controllers and electronic components help identify signs of corrosion or potential issues. Any corrosion found should be addressed promptly.
- **Preventive Maintenance:** Implementing a preventive maintenance schedule, including cleaning and inspecting components, helps prevent corrosion and ensures the longevity of the equipment.
8. **Cathodic Protection (For Metallic Components):**
- **Sacrificial Anodes:** In environments where corrosion is a significant concern, sacrificial anodes made of a more reactive metal may be installed. These anodes corrode instead of the critical components, protecting them from damage.
Implementing a combination of these measures helps create a robust defense against corrosion, ensuring the reliable and effective performance of fire pump controllers and associated electronic components over time.
1. **Enclosures and Sealing:**
- **Weatherproof Enclosures:** Fire pump controllers are often housed in weatherproof enclosures that protect the electronic components from environmental elements such as rain, snow, and humidity.
- **IP Ratings:** Enclosures are designed with specific Ingress Protection (IP) ratings to indicate their resistance to moisture and dust. Higher IP ratings provide better protection against environmental factors.
2. **Corrosion-Resistant Materials:**
- **Component Selection:** Choosing electronic components and materials that are corrosion-resistant is essential. This includes using corrosion-resistant metals, coatings, and materials for the construction of the controllers.
3. **Sealed Connectors and Joints:**
- **Sealed Connectors:** Electrical connectors should be designed to be water-resistant or waterproof to prevent moisture ingress.
- **Joints and Seams:** Proper sealing of joints and seams in the enclosure helps prevent water infiltration. Gaskets, seals, and adhesives may be used for this purpose.
4. **Coatings and Finishes:**
- **Protective Coatings:** Applying protective coatings to electronic components and surfaces can help prevent corrosion. This may include coatings with corrosion-resistant properties, such as epoxy or other specialized coatings.
- **Powder Coating:** Some controllers may have a powder-coated finish, which provides an additional layer of protection against corrosion.
5. **Ventilation and Air Circulation:**
- **Proper Ventilation:** Adequate ventilation is essential to prevent condensation inside the enclosure. Proper airflow helps maintain a more stable internal environment, reducing the risk of moisture-related corrosion.
6. **Environmental Monitoring:**
- **Humidity Sensors:** Installing humidity sensors within the enclosure allows for monitoring and controlling the humidity levels. This information can trigger alarms or actions to mitigate excessive moisture.
7. **Regular Inspections and Maintenance:**
- **Scheduled Inspections:** Regular inspections of fire pump controllers and electronic components help identify signs of corrosion or potential issues. Any corrosion found should be addressed promptly.
- **Preventive Maintenance:** Implementing a preventive maintenance schedule, including cleaning and inspecting components, helps prevent corrosion and ensures the longevity of the equipment.
8. **Cathodic Protection (For Metallic Components):**
- **Sacrificial Anodes:** In environments where corrosion is a significant concern, sacrificial anodes made of a more reactive metal may be installed. These anodes corrode instead of the critical components, protecting them from damage.
Implementing a combination of these measures helps create a robust defense against corrosion, ensuring the reliable and effective performance of fire pump controllers and associated electronic components over time.
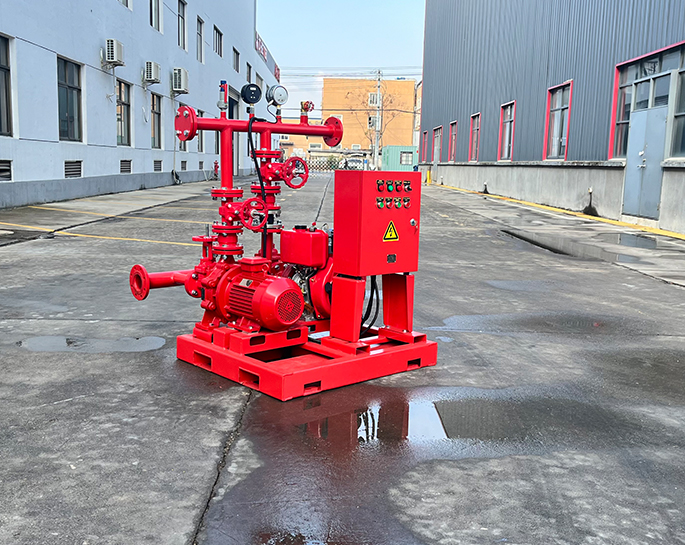