What is cavitation in fire pumps, and how can it be prevented?
May 28, 2024
Share:
Cavitation in fire pumps refers to the formation and subsequent collapse of vapor bubbles in the pump's liquid flow, which can cause significant damage to the pump components. This phenomenon occurs when the local pressure in the pump falls below the liquid's vapor pressure, leading to the formation of vapor bubbles. When these bubbles move to higher-pressure areas within the pump, they collapse violently, causing shock waves that can erode metal surfaces and impair the pump's performance.
### Causes of Cavitation in Fire Pumps
1. **Low Suction Pressure**: Inadequate pressure at the pump's suction side can lead to cavitation.
2. **High Pump Speed**: Running the pump at excessively high speeds can reduce pressure on the suction side, promoting cavitation.
3. **High Fluid Temperature**: Higher temperatures lower the liquid's vapor pressure, making cavitation more likely.
4. **Improper Pump Selection**: Using a pump that is not suited for the specific operational conditions can result in cavitation.
5. **Obstructed Suction Line**: Blockages or restrictions in the suction line can reduce pressure and cause cavitation.
### Effects of Cavitation
- **Erosion of Pump Components**: Repeated bubble collapse erodes impellers, casings, and other internal surfaces.
- **Reduced Pump Efficiency**: Cavitation disrupts smooth flow, reducing the pump's efficiency and flow rate.
- **Increased Vibration and Noise**: The collapsing bubbles cause vibration and noise, indicating potential cavitation.
- **Mechanical Damage**: Prolonged cavitation can lead to mechanical failure of pump components.
### Preventing Cavitation in Fire Pumps
1. **Ensure Proper NPSH (Net Positive Suction Head)**:
- **Adequate NPSH Available (NPSHa)**: Ensure that the system provides sufficient pressure at the pump suction to avoid falling below vapor pressure.
- **Calculate NPSH Requirements**: Verify that the NPSHa is greater than the NPSH Required (NPSHr) by the pump.
2. **Maintain Suction Line Conditions**:
- **Properly Sized Suction Lines**: Ensure suction lines are of adequate diameter to minimize pressure drop.
- **Avoid Obstructions**: Keep suction lines free from debris, blockages, and restrictions.
- **Short and Straight Suction Lines**: Design suction lines to be as short and straight as possible to reduce pressure losses.
3. **Control Fluid Temperature**:
- **Cool the Fluid**: Use cooling methods if the liquid temperature is too high, potentially including heat exchangers.
- **Avoid Excessive Heating**: Prevent the liquid from heating excessively due to external conditions or internal friction.
4. **Optimal Pump Speed**:
- **Adjust Pump Speed**: Operate the pump within recommended speed ranges to avoid excessive low pressure at the suction.
5. **Proper Pump Selection**:
- **Match Pump to Application**: Choose a pump designed to handle the specific conditions of the system, including flow rate, pressure, and fluid characteristics.
- **Use Correct Impeller Design**: Select impellers designed to minimize cavitation, such as those with inducer blades.
6. **Regular Maintenance and Inspection**:
- **Routine Checks**: Regularly inspect and maintain pump components and suction lines to ensure they are in good working condition.
- **Replace Worn Parts**: Promptly replace any worn or damaged parts to maintain optimal pump performance.
By understanding the causes of cavitation and implementing these preventive measures, the likelihood of cavitation in fire pumps can be significantly reduced, ensuring reliable and efficient operation.
### Causes of Cavitation in Fire Pumps
1. **Low Suction Pressure**: Inadequate pressure at the pump's suction side can lead to cavitation.
2. **High Pump Speed**: Running the pump at excessively high speeds can reduce pressure on the suction side, promoting cavitation.
3. **High Fluid Temperature**: Higher temperatures lower the liquid's vapor pressure, making cavitation more likely.
4. **Improper Pump Selection**: Using a pump that is not suited for the specific operational conditions can result in cavitation.
5. **Obstructed Suction Line**: Blockages or restrictions in the suction line can reduce pressure and cause cavitation.
### Effects of Cavitation
- **Erosion of Pump Components**: Repeated bubble collapse erodes impellers, casings, and other internal surfaces.
- **Reduced Pump Efficiency**: Cavitation disrupts smooth flow, reducing the pump's efficiency and flow rate.
- **Increased Vibration and Noise**: The collapsing bubbles cause vibration and noise, indicating potential cavitation.
- **Mechanical Damage**: Prolonged cavitation can lead to mechanical failure of pump components.
### Preventing Cavitation in Fire Pumps
1. **Ensure Proper NPSH (Net Positive Suction Head)**:
- **Adequate NPSH Available (NPSHa)**: Ensure that the system provides sufficient pressure at the pump suction to avoid falling below vapor pressure.
- **Calculate NPSH Requirements**: Verify that the NPSHa is greater than the NPSH Required (NPSHr) by the pump.
2. **Maintain Suction Line Conditions**:
- **Properly Sized Suction Lines**: Ensure suction lines are of adequate diameter to minimize pressure drop.
- **Avoid Obstructions**: Keep suction lines free from debris, blockages, and restrictions.
- **Short and Straight Suction Lines**: Design suction lines to be as short and straight as possible to reduce pressure losses.
3. **Control Fluid Temperature**:
- **Cool the Fluid**: Use cooling methods if the liquid temperature is too high, potentially including heat exchangers.
- **Avoid Excessive Heating**: Prevent the liquid from heating excessively due to external conditions or internal friction.
4. **Optimal Pump Speed**:
- **Adjust Pump Speed**: Operate the pump within recommended speed ranges to avoid excessive low pressure at the suction.
5. **Proper Pump Selection**:
- **Match Pump to Application**: Choose a pump designed to handle the specific conditions of the system, including flow rate, pressure, and fluid characteristics.
- **Use Correct Impeller Design**: Select impellers designed to minimize cavitation, such as those with inducer blades.
6. **Regular Maintenance and Inspection**:
- **Routine Checks**: Regularly inspect and maintain pump components and suction lines to ensure they are in good working condition.
- **Replace Worn Parts**: Promptly replace any worn or damaged parts to maintain optimal pump performance.
By understanding the causes of cavitation and implementing these preventive measures, the likelihood of cavitation in fire pumps can be significantly reduced, ensuring reliable and efficient operation.
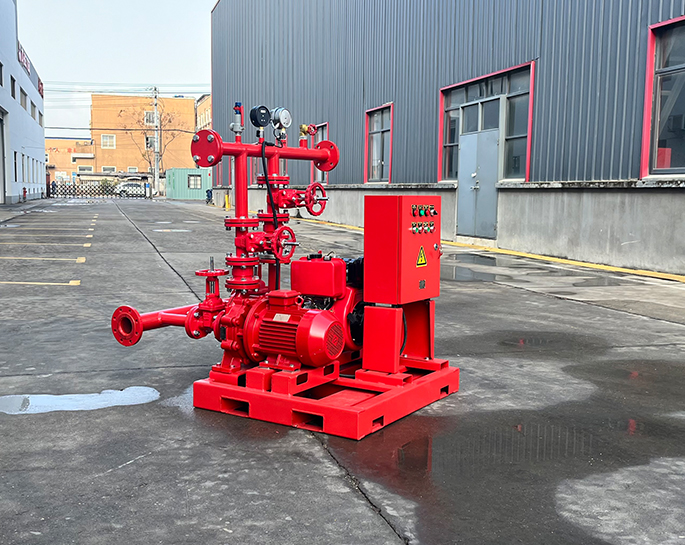