What are the requirements for maintaining a centrifugal pump and what to do when the centrifugal pump stops running?
Jan 30, 2023
Share:
The unpainted surface of the pump that has not been installed should be coated with a suitable anti-rust agent. Bearings lubricated with oil should be filled with a suitable oil. Bearings lubricated with grease should only be filled with a grease, do not use Mix grease.
Pump clean liquid for a short time, rinse, suction line, discharge line, pump casing and impeller, and drain flushing fluid in pump casing, suction line and discharge line.
Drain the oil from the bearing housing, refill with clean oil, thoroughly clean the grease and refill with new grease.
Seal the suction port and discharge port, store the pump in a clean, dry place, protect the motor windings from moisture, and spray the inside of the pump casing with anti-rust and anti-corrosion liquid.
Rotate the pump shaft once a month to avoid freezing and lubricate the bearings.
After the centrifugal pump stops running, the inlet valve of the pump should be closed, and the valves of the auxiliary system should be closed in turn after the pump cools down.
High-temperature pump parking should be carried out in accordance with the provisions of the equipment technical documents. After parking, it should be cranked for half a circle every 20 to 30 minutes until the temperature of the pump body drops to 50°C.
When the cryogenic pump is stopped, the pump should always be filled with liquid unless there are special requirements; the suction valve and discharge valve should be kept open; for cryogenic pumps with double-end mechanical seals, the liquid level controller and the sealing liquid in the pump seal chamber should be Maintain pump grout pressure.
For pumps transporting media that are prone to crystallization, solidification, and precipitation, prevent blockage after stopping the pump, and flush the pump and pipeline with clean water or other media in time.
Drain the liquid accumulated in the pump to prevent rust and frost cracking.
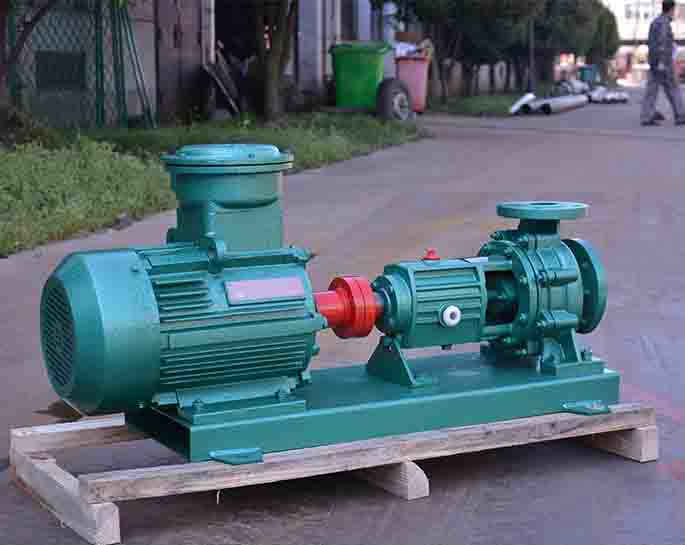
Pump clean liquid for a short time, rinse, suction line, discharge line, pump casing and impeller, and drain flushing fluid in pump casing, suction line and discharge line.
Drain the oil from the bearing housing, refill with clean oil, thoroughly clean the grease and refill with new grease.
Seal the suction port and discharge port, store the pump in a clean, dry place, protect the motor windings from moisture, and spray the inside of the pump casing with anti-rust and anti-corrosion liquid.
Rotate the pump shaft once a month to avoid freezing and lubricate the bearings.
After the centrifugal pump stops running, the inlet valve of the pump should be closed, and the valves of the auxiliary system should be closed in turn after the pump cools down.
High-temperature pump parking should be carried out in accordance with the provisions of the equipment technical documents. After parking, it should be cranked for half a circle every 20 to 30 minutes until the temperature of the pump body drops to 50°C.
When the cryogenic pump is stopped, the pump should always be filled with liquid unless there are special requirements; the suction valve and discharge valve should be kept open; for cryogenic pumps with double-end mechanical seals, the liquid level controller and the sealing liquid in the pump seal chamber should be Maintain pump grout pressure.
For pumps transporting media that are prone to crystallization, solidification, and precipitation, prevent blockage after stopping the pump, and flush the pump and pipeline with clean water or other media in time.
Drain the liquid accumulated in the pump to prevent rust and frost cracking.
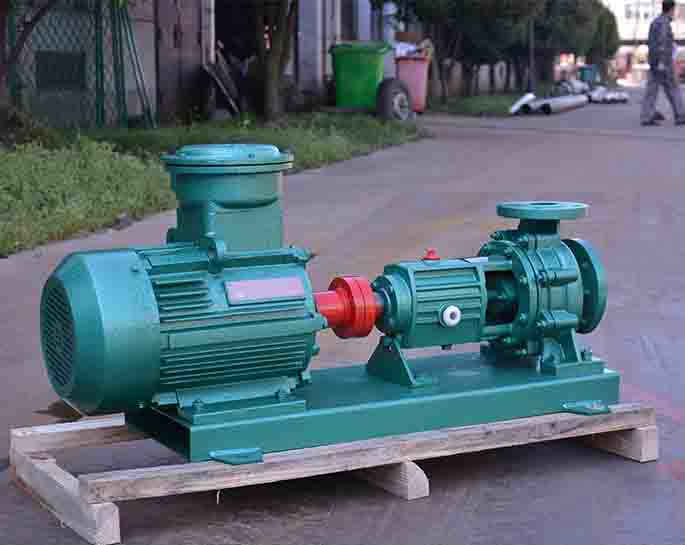