What are the key considerations for fire pump installation in hazardous locations?
Aug 29, 2024
Share:
Installing fire pumps in hazardous locations requires careful consideration of safety, compliance, and operational requirements. Here are some key considerations:
### 1. **Classification of Hazardous Location**
- **Determine the Classification**: Identify the specific classification of the hazardous area where the fire pump will be installed. Hazardous locations are categorized into classes, divisions (or zones), and groups based on the presence of flammable gases, vapors, dust, or fibers.
- **Classes and Divisions/Zones**:
- **Class I**: Locations where flammable gases or vapors may be present in sufficient quantities to produce explosive or ignitable mixtures (e.g., oil refineries, chemical plants).
- **Class II**: Areas where combustible dust is present (e.g., grain elevators, flour mills).
- **Class III**: Locations where ignitable fibers or flyings are present (e.g., textile mills, woodworking facilities).
- **Divisions** (in North America) or **Zones** (internationally) indicate the likelihood of hazardous substances being present under normal or abnormal conditions.
### 2. **Compliance with Standards and Codes**
- **NFPA Standards**: Follow the National Fire Protection Association (NFPA) standards, specifically NFPA 20 (Standard for the Installation of Stationary Pumps for Fire Protection) and NFPA 70 (National Electrical Code) for electrical requirements in hazardous locations.
- **UL/FM Approval**: Ensure fire pumps and their components are UL (Underwriters Laboratories) listed or FM (Factory Mutual) approved for use in the specific hazardous location.
- **ATEX Certification**: In Europe, equipment must comply with ATEX (Atmosphères Explosibles) directives, ensuring it is safe for explosive atmospheres.
### 3. **Electrical and Mechanical Considerations**
- **Explosion-Proof Equipment**: Use explosion-proof electrical equipment and enclosures to prevent ignition sources in hazardous areas.
- **Ingress Protection (IP) Rating**: Ensure that electrical components have an appropriate IP rating to prevent the ingress of dust or moisture that could cause malfunctions or explosions.
- **Corrosion Resistance**: Use materials and coatings that are resistant to corrosive substances often found in hazardous environments.
- **Grounding and Bonding**: Proper grounding and bonding of all metallic components to prevent static discharge, which could ignite flammable substances.
### 4. **Location and Accessibility**
- **Safe Distance**: Install fire pumps away from the immediate hazard area whenever possible, maintaining safe distances from potential ignition sources.
- **Ventilation**: Ensure proper ventilation to avoid accumulation of flammable gases or dust in enclosed spaces.
- **Ease of Maintenance**: Design the installation to provide easy access for maintenance and inspection while ensuring safety protocols are in place.
### 5. **Control Systems and Monitoring**
- **Intrinsically Safe Systems**: Utilize intrinsically safe control systems and devices that prevent sparks or heat that could cause ignition in hazardous areas.
- **Remote Monitoring**: Install systems that allow for remote monitoring and control to reduce the need for personnel to enter hazardous areas.
- **Fire Pump Controller**: Use controllers specifically designed and approved for hazardous locations, equipped with protective features against electrical faults.
### 6. **Emergency and Safety Procedures**
- **Emergency Shutoff**: Include emergency shutoff mechanisms that can be activated from a safe distance.
- **Training and Preparedness**: Ensure that personnel are trained in safety procedures specific to hazardous locations and fire pump operation.
- **Regular Inspections**: Implement routine inspections and maintenance checks to ensure all equipment remains in proper working condition.
### 7. **Environmental Conditions**
- **Temperature Control**: Consider temperature control to avoid conditions that could lead to auto-ignition of flammable substances.
- **Humidity and Weather Protection**: Protect equipment from environmental factors like humidity, rain, and extreme temperatures, which can affect performance and safety.
By adhering to these key considerations, you can ensure the safe and effective installation of fire pumps in hazardous locations, minimizing the risk of fire or explosion while maintaining compliance with applicable safety standards and regulations.
### 1. **Classification of Hazardous Location**
- **Determine the Classification**: Identify the specific classification of the hazardous area where the fire pump will be installed. Hazardous locations are categorized into classes, divisions (or zones), and groups based on the presence of flammable gases, vapors, dust, or fibers.
- **Classes and Divisions/Zones**:
- **Class I**: Locations where flammable gases or vapors may be present in sufficient quantities to produce explosive or ignitable mixtures (e.g., oil refineries, chemical plants).
- **Class II**: Areas where combustible dust is present (e.g., grain elevators, flour mills).
- **Class III**: Locations where ignitable fibers or flyings are present (e.g., textile mills, woodworking facilities).
- **Divisions** (in North America) or **Zones** (internationally) indicate the likelihood of hazardous substances being present under normal or abnormal conditions.
### 2. **Compliance with Standards and Codes**
- **NFPA Standards**: Follow the National Fire Protection Association (NFPA) standards, specifically NFPA 20 (Standard for the Installation of Stationary Pumps for Fire Protection) and NFPA 70 (National Electrical Code) for electrical requirements in hazardous locations.
- **UL/FM Approval**: Ensure fire pumps and their components are UL (Underwriters Laboratories) listed or FM (Factory Mutual) approved for use in the specific hazardous location.
- **ATEX Certification**: In Europe, equipment must comply with ATEX (Atmosphères Explosibles) directives, ensuring it is safe for explosive atmospheres.
### 3. **Electrical and Mechanical Considerations**
- **Explosion-Proof Equipment**: Use explosion-proof electrical equipment and enclosures to prevent ignition sources in hazardous areas.
- **Ingress Protection (IP) Rating**: Ensure that electrical components have an appropriate IP rating to prevent the ingress of dust or moisture that could cause malfunctions or explosions.
- **Corrosion Resistance**: Use materials and coatings that are resistant to corrosive substances often found in hazardous environments.
- **Grounding and Bonding**: Proper grounding and bonding of all metallic components to prevent static discharge, which could ignite flammable substances.
### 4. **Location and Accessibility**
- **Safe Distance**: Install fire pumps away from the immediate hazard area whenever possible, maintaining safe distances from potential ignition sources.
- **Ventilation**: Ensure proper ventilation to avoid accumulation of flammable gases or dust in enclosed spaces.
- **Ease of Maintenance**: Design the installation to provide easy access for maintenance and inspection while ensuring safety protocols are in place.
### 5. **Control Systems and Monitoring**
- **Intrinsically Safe Systems**: Utilize intrinsically safe control systems and devices that prevent sparks or heat that could cause ignition in hazardous areas.
- **Remote Monitoring**: Install systems that allow for remote monitoring and control to reduce the need for personnel to enter hazardous areas.
- **Fire Pump Controller**: Use controllers specifically designed and approved for hazardous locations, equipped with protective features against electrical faults.
### 6. **Emergency and Safety Procedures**
- **Emergency Shutoff**: Include emergency shutoff mechanisms that can be activated from a safe distance.
- **Training and Preparedness**: Ensure that personnel are trained in safety procedures specific to hazardous locations and fire pump operation.
- **Regular Inspections**: Implement routine inspections and maintenance checks to ensure all equipment remains in proper working condition.
### 7. **Environmental Conditions**
- **Temperature Control**: Consider temperature control to avoid conditions that could lead to auto-ignition of flammable substances.
- **Humidity and Weather Protection**: Protect equipment from environmental factors like humidity, rain, and extreme temperatures, which can affect performance and safety.
By adhering to these key considerations, you can ensure the safe and effective installation of fire pumps in hazardous locations, minimizing the risk of fire or explosion while maintaining compliance with applicable safety standards and regulations.
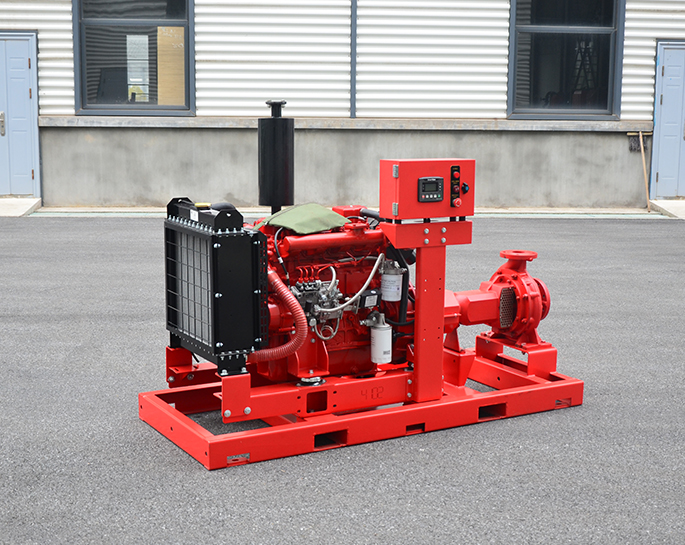