How do fire pump suppliers ensure product quality and reliability throughout the lifecycle of their equipment?
Mar 04, 2024
Share:
Fire pump suppliers ensure product quality and reliability throughout the lifecycle of their equipment through various measures:
1. **Quality Management Systems (QMS)**: Implementing robust quality management systems such as ISO 9001 helps ensure that all aspects of the manufacturing process adhere to stringent quality standards. This involves establishing clear quality objectives, conducting regular audits, and continuously monitoring and improving processes.
2. **Supplier Quality Assurance**: Selecting reputable suppliers and conducting thorough supplier assessments ensures that components and materials used in the manufacturing process meet quality specifications. This may involve performing supplier audits, conducting quality inspections upon receipt of materials, and maintaining open communication with suppliers to address any quality issues.
3. **Design and Engineering Standards**: Adhering to industry standards and best practices in product design and engineering helps ensure that fire pump equipment meets or exceeds performance and safety requirements. This involves conducting thorough design reviews, performing risk assessments, and incorporating feedback from testing and validation processes.
4. **Testing and Validation**: Conducting comprehensive testing and validation procedures throughout the product development lifecycle helps identify potential issues and verify that equipment meets performance and reliability requirements. This includes conducting functional tests, performance tests, durability tests, and reliability testing under various operating conditions.
5. **Quality Control Inspections**: Implementing stringent quality control inspections at key stages of the manufacturing process helps detect and address any defects or deviations from specifications. This involves conducting in-process inspections, final product inspections, and quality checks before shipping equipment to customers.
6. **Continuous Monitoring and Feedback**: Establishing processes for monitoring product performance and collecting feedback from customers helps identify any quality or reliability issues that may arise during the equipment's lifecycle. This includes conducting field tests, collecting data on equipment performance, and maintaining open communication channels with customers to address any concerns.
7. **Lifecycle Support and Maintenance**: Providing comprehensive lifecycle support and maintenance services ensures that fire pump equipment remains reliable and performs optimally throughout its service life. This includes offering preventive maintenance programs, spare parts availability, technical support, and training for maintenance personnel.
8. **Continuous Improvement**: Implementing processes for continuous improvement allows fire pump suppliers to identify opportunities to enhance product quality and reliability over time. This involves analyzing data on product performance, conducting root cause analysis for any quality issues, and implementing corrective and preventive actions to address them.
By implementing these measures, fire pump suppliers can ensure that their equipment meets high standards of quality and reliability throughout its lifecycle, ultimately enhancing customer satisfaction and maintaining a strong reputation in the market.
1. **Quality Management Systems (QMS)**: Implementing robust quality management systems such as ISO 9001 helps ensure that all aspects of the manufacturing process adhere to stringent quality standards. This involves establishing clear quality objectives, conducting regular audits, and continuously monitoring and improving processes.
2. **Supplier Quality Assurance**: Selecting reputable suppliers and conducting thorough supplier assessments ensures that components and materials used in the manufacturing process meet quality specifications. This may involve performing supplier audits, conducting quality inspections upon receipt of materials, and maintaining open communication with suppliers to address any quality issues.
3. **Design and Engineering Standards**: Adhering to industry standards and best practices in product design and engineering helps ensure that fire pump equipment meets or exceeds performance and safety requirements. This involves conducting thorough design reviews, performing risk assessments, and incorporating feedback from testing and validation processes.
4. **Testing and Validation**: Conducting comprehensive testing and validation procedures throughout the product development lifecycle helps identify potential issues and verify that equipment meets performance and reliability requirements. This includes conducting functional tests, performance tests, durability tests, and reliability testing under various operating conditions.
5. **Quality Control Inspections**: Implementing stringent quality control inspections at key stages of the manufacturing process helps detect and address any defects or deviations from specifications. This involves conducting in-process inspections, final product inspections, and quality checks before shipping equipment to customers.
6. **Continuous Monitoring and Feedback**: Establishing processes for monitoring product performance and collecting feedback from customers helps identify any quality or reliability issues that may arise during the equipment's lifecycle. This includes conducting field tests, collecting data on equipment performance, and maintaining open communication channels with customers to address any concerns.
7. **Lifecycle Support and Maintenance**: Providing comprehensive lifecycle support and maintenance services ensures that fire pump equipment remains reliable and performs optimally throughout its service life. This includes offering preventive maintenance programs, spare parts availability, technical support, and training for maintenance personnel.
8. **Continuous Improvement**: Implementing processes for continuous improvement allows fire pump suppliers to identify opportunities to enhance product quality and reliability over time. This involves analyzing data on product performance, conducting root cause analysis for any quality issues, and implementing corrective and preventive actions to address them.
By implementing these measures, fire pump suppliers can ensure that their equipment meets high standards of quality and reliability throughout its lifecycle, ultimately enhancing customer satisfaction and maintaining a strong reputation in the market.
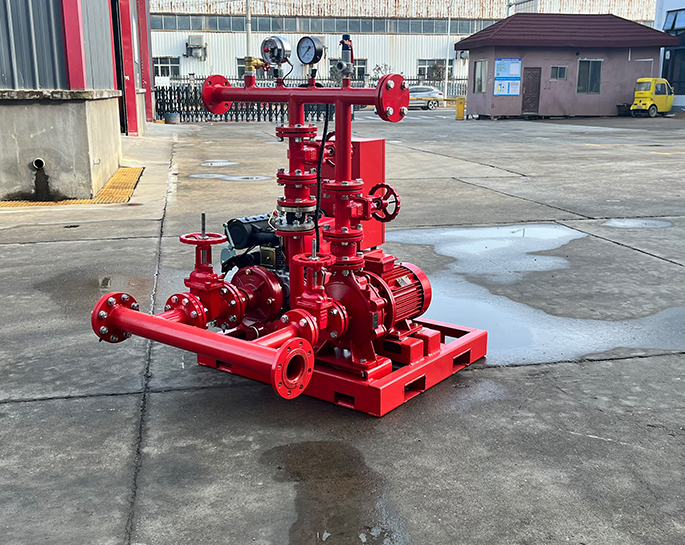