Fire pump power saving measures and how to make the fire pump run smoothly
Dec 27, 2022
Share:
1. Adopt high-efficiency and energy-saving water pumps and high-efficiency and low-loss motors, and improve the efficiency of transmission devices.
2. Correctly select the power of the pump motor. Prevent "big horses and small carts". Replace the overcapacity water pump motor. When the power of the motor is much greater than the actual need, the method of replacing the motor can be used to save electricity.
3. Choose a reasonable lift. When the head of the pump leaves too much margin. It will waste electric energy, so the head of the pump's operating point should be reasonably determined. 4. Reduce pipeline resistance. Eliminate redundant pipe fittings, unnecessary turns and sharp angles on the pipeline to reduce pipeline resistance and reduce unit power consumption for water delivery.
The methods to reduce pipeline resistance include:
①. Pipeline design should be reasonable.
②. Increase the pipe diameter or use double pipe drainage to reduce the flow rate.
③. Shorten the length of the pipeline as much as possible, reduce joints, elbows and valves, and especially avoid the appearance of sharp angles.
④. Improve the smoothness of the inner wall of the pipeline or add a coating.
⑤. Remove the dirt on the inner wall of the pipeline in time.
5. Water pump speed regulation saves electricity. The power consumption of the water pump is proportional to the cube of the speed of the unit, so the speed of the unit should be changed according to the actual load conditions. Can greatly save electric energy. Adopting pump speed regulation measures, the initial investment is relatively large, but the power saving effect is remarkable, especially suitable for large-capacity water pumps. It should be noted that the larger the head, the flatter the resistance curve, even if the speed changes slightly, the flow rate will change greatly, and the power saving effect is poor.
6. Transform the pump impeller. When the flow rate of the pump in use is larger than the actual flow rate required, and the speed control cannot be used or the price of the speed control device is uneconomical, the impeller of the original pump can be turned or replaced to reduce the flow rate and Head, in order to reduce the running power consumption of the pump.
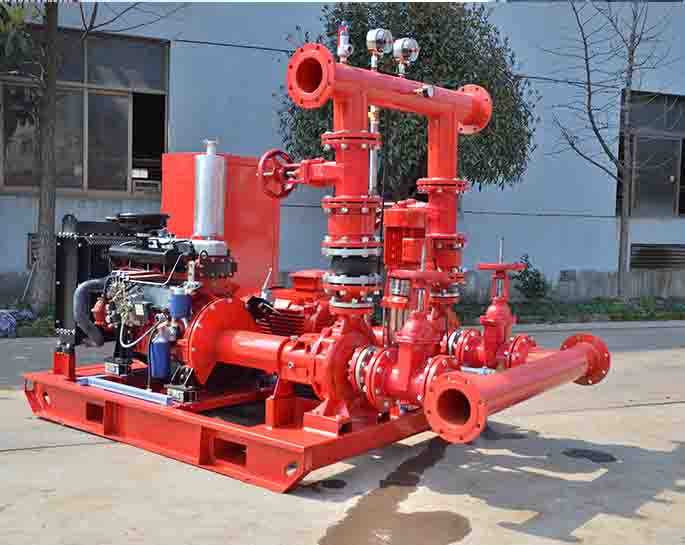
If the feedwater pump is designed using the same conversion method, after obtaining the speed n of the required operating conditions, the individual arcs of the corresponding operating conditions can be converted according to the formula: or the rotating speed and multi-stage The characteristic curve of the fire pump's initial and final operating conditions is the first step in the design and calculation of the feed water pump. In order to make the feed water pump run quietly and reliably under all operating conditions, the extremely serious condition is to ensure that no cavitation occurs under each operating condition, and the guarantee condition for no cavitation should be given by the front Booster pump supply for the water pump. Design and calculation of pre-boosted fire pump The pre-boosted pump is referred to as the booster pump for short, it is placed before the suction of the boiler feed water pump, and provides the feed water pump with sufficient suction pressure to avoid cavitation under operating conditions . Before designing and calculating the booster pump, it is necessary to first confirm the design calculation flow and head value of the single-stage fire pump. It is precisely because of the connection between the booster pump and the feedwater pump that the exact design and calculation parameters of the booster pump are all related to the corresponding working condition parameters of the feedwater pump.
The impeller is eccentrically installed in the pump body. When the impeller rotates according to the correct direction, the water entering the fire pump body is thrown to the limit by the impeller. Due to the influence of centrifugal force, the water forms a uniform thickness similar to the pump cavity. closed water ring. The upper inner surface of the water ring happens to be tangent to the impeller hub, and the lower inner surface of the water ring just meets the top of the blades (actually, the blades have a certain insertion depth in the water ring). At this time, a crescent-shaped space is formed between the hub of the impeller and the water ring, and this space is divided into several small cavities equal to the number of blades by the impeller. If starting from the upper part of the impeller at 0°, then when the impeller of the fire pump rotates 180° before the rotation, the volume of the small chamber gradually increases from small to large, the pressure decreases continuously, and it communicates with the suction port on the suction and exhaust pan , when the pressure in the small chamber space is lower than the pressure in the pumped container, according to the principle of gas pressure balance, the pumped gas is continuously drawn into the small chamber, and it is in the process of inhalation.
When the inhalation is completed, it is isolated from the inhalation port, the volume of the small cavity is gradually decreasing, and the pressure is continuously increasing. exhaust. And the volume of the small cavity communicated with the exhaust port further reduces the pressure to further promote. When the pressure of the gas is stronger than the exhaust pressure, the compressed gas is discharged from the exhaust port. During the continuous operation of the pump, Continuously carry out the process of suction, compression and exhaust, so as to achieve the purpose of continuous pumping.
In the water ring pump, the auxiliary exhaust valve is a special structure, generally using a rubber ball valve, its function is to submerge the phenomenon of over-compression and under-compression generated during the operation of the pump. Both phenomena will cause excessive power consumption. In order to solve this problem, a rubber ball valve is generally installed under the exhaust port, so that when the fire pump chamber reaches the exhaust pressure prematurely, the ball valve will automatically open and the gas will be discharged, eliminating the over-compression phenomenon. Generally, when designing a water ring pump, the minimum suction pressure is used to determine the compression ratio, so as to determine the starting position of the exhaust port, so as to solve the phenomenon of insufficient compression.
2. Correctly select the power of the pump motor. Prevent "big horses and small carts". Replace the overcapacity water pump motor. When the power of the motor is much greater than the actual need, the method of replacing the motor can be used to save electricity.
3. Choose a reasonable lift. When the head of the pump leaves too much margin. It will waste electric energy, so the head of the pump's operating point should be reasonably determined. 4. Reduce pipeline resistance. Eliminate redundant pipe fittings, unnecessary turns and sharp angles on the pipeline to reduce pipeline resistance and reduce unit power consumption for water delivery.
The methods to reduce pipeline resistance include:
①. Pipeline design should be reasonable.
②. Increase the pipe diameter or use double pipe drainage to reduce the flow rate.
③. Shorten the length of the pipeline as much as possible, reduce joints, elbows and valves, and especially avoid the appearance of sharp angles.
④. Improve the smoothness of the inner wall of the pipeline or add a coating.
⑤. Remove the dirt on the inner wall of the pipeline in time.
5. Water pump speed regulation saves electricity. The power consumption of the water pump is proportional to the cube of the speed of the unit, so the speed of the unit should be changed according to the actual load conditions. Can greatly save electric energy. Adopting pump speed regulation measures, the initial investment is relatively large, but the power saving effect is remarkable, especially suitable for large-capacity water pumps. It should be noted that the larger the head, the flatter the resistance curve, even if the speed changes slightly, the flow rate will change greatly, and the power saving effect is poor.
6. Transform the pump impeller. When the flow rate of the pump in use is larger than the actual flow rate required, and the speed control cannot be used or the price of the speed control device is uneconomical, the impeller of the original pump can be turned or replaced to reduce the flow rate and Head, in order to reduce the running power consumption of the pump.
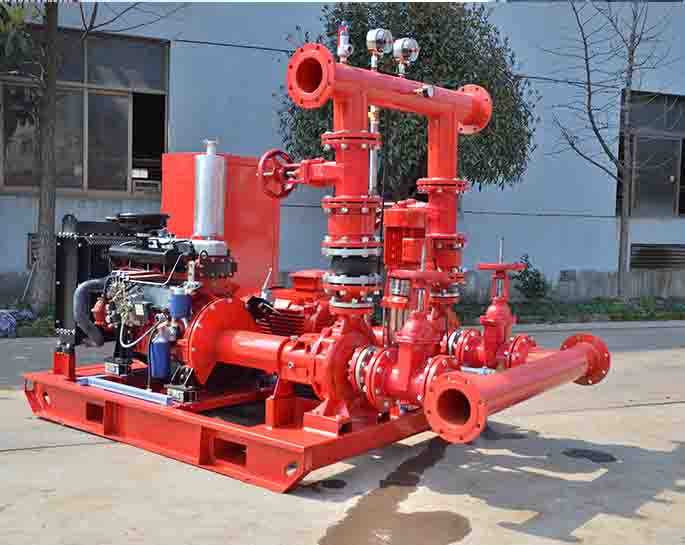
If the feedwater pump is designed using the same conversion method, after obtaining the speed n of the required operating conditions, the individual arcs of the corresponding operating conditions can be converted according to the formula: or the rotating speed and multi-stage The characteristic curve of the fire pump's initial and final operating conditions is the first step in the design and calculation of the feed water pump. In order to make the feed water pump run quietly and reliably under all operating conditions, the extremely serious condition is to ensure that no cavitation occurs under each operating condition, and the guarantee condition for no cavitation should be given by the front Booster pump supply for the water pump. Design and calculation of pre-boosted fire pump The pre-boosted pump is referred to as the booster pump for short, it is placed before the suction of the boiler feed water pump, and provides the feed water pump with sufficient suction pressure to avoid cavitation under operating conditions . Before designing and calculating the booster pump, it is necessary to first confirm the design calculation flow and head value of the single-stage fire pump. It is precisely because of the connection between the booster pump and the feedwater pump that the exact design and calculation parameters of the booster pump are all related to the corresponding working condition parameters of the feedwater pump.
The impeller is eccentrically installed in the pump body. When the impeller rotates according to the correct direction, the water entering the fire pump body is thrown to the limit by the impeller. Due to the influence of centrifugal force, the water forms a uniform thickness similar to the pump cavity. closed water ring. The upper inner surface of the water ring happens to be tangent to the impeller hub, and the lower inner surface of the water ring just meets the top of the blades (actually, the blades have a certain insertion depth in the water ring). At this time, a crescent-shaped space is formed between the hub of the impeller and the water ring, and this space is divided into several small cavities equal to the number of blades by the impeller. If starting from the upper part of the impeller at 0°, then when the impeller of the fire pump rotates 180° before the rotation, the volume of the small chamber gradually increases from small to large, the pressure decreases continuously, and it communicates with the suction port on the suction and exhaust pan , when the pressure in the small chamber space is lower than the pressure in the pumped container, according to the principle of gas pressure balance, the pumped gas is continuously drawn into the small chamber, and it is in the process of inhalation.
When the inhalation is completed, it is isolated from the inhalation port, the volume of the small cavity is gradually decreasing, and the pressure is continuously increasing. exhaust. And the volume of the small cavity communicated with the exhaust port further reduces the pressure to further promote. When the pressure of the gas is stronger than the exhaust pressure, the compressed gas is discharged from the exhaust port. During the continuous operation of the pump, Continuously carry out the process of suction, compression and exhaust, so as to achieve the purpose of continuous pumping.
In the water ring pump, the auxiliary exhaust valve is a special structure, generally using a rubber ball valve, its function is to submerge the phenomenon of over-compression and under-compression generated during the operation of the pump. Both phenomena will cause excessive power consumption. In order to solve this problem, a rubber ball valve is generally installed under the exhaust port, so that when the fire pump chamber reaches the exhaust pressure prematurely, the ball valve will automatically open and the gas will be discharged, eliminating the over-compression phenomenon. Generally, when designing a water ring pump, the minimum suction pressure is used to determine the compression ratio, so as to determine the starting position of the exhaust port, so as to solve the phenomenon of insufficient compression.