Common causes of fire pump mechanical seal leakage
Jul 12, 2023
Share:
There are several common causes of mechanical seal leakage in fire pumps. Some of the primary factors that can contribute to mechanical seal leakage include:
Seal Damage or Wear: Mechanical seals can become damaged or worn over time due to factors such as excessive pressure, misalignment, abrasive particles in the pumped fluid, or insufficient lubrication. This can lead to gaps or cracks in the seal, resulting in leakage.
Incorrect Installation: Improper installation of the mechanical seal can compromise its effectiveness and lead to leakage. This can include incorrect alignment of the seal components, insufficient tightening of fasteners, or improper use of sealants or gaskets.
Seal Face Misalignment: If the seal faces are not properly aligned, they may not make adequate contact with each other, resulting in a poor seal. Misalignment can be caused by factors such as shaft deflection, bearing wear, or improper installation.
Excessive Shaft Movement: Excessive axial or radial movement of the pump shaft can cause mechanical seal leakage. This movement can be due to factors such as worn bearings, improper coupling alignment, or excessive vibration in the pump system.
Contaminants in the Pumped Fluid: Abrasive particles, chemicals, or solids present in the pumped fluid can damage the seal faces and compromise their ability to create an effective seal. This can lead to leakage over time.
Insufficient Lubrication or Cooling: Mechanical seals require proper lubrication and cooling to operate effectively. Inadequate lubrication or cooling can cause excessive friction, heat buildup, and accelerated wear of the seal components, resulting in leakage.
Seal Material Incompatibility: Using a mechanical seal made from incompatible materials for the pumped fluid can lead to seal degradation and leakage. It is important to select seal materials that are compatible with the characteristics of the fluid being pumped, including its temperature, pH, and chemical composition.
Operating Conditions: Extreme operating conditions, such as high temperatures, high pressures, or frequent starts and stops, can put additional stress on the mechanical seal and increase the risk of leakage.
Regular inspection, proper maintenance, and adherence to manufacturer guidelines for installation and operation can help minimize mechanical seal leakage in fire pumps. Additionally, using high-quality seals appropriate for the specific application and maintaining proper fluid cleanliness can also contribute to reducing seal leakage.
Seal Damage or Wear: Mechanical seals can become damaged or worn over time due to factors such as excessive pressure, misalignment, abrasive particles in the pumped fluid, or insufficient lubrication. This can lead to gaps or cracks in the seal, resulting in leakage.
Incorrect Installation: Improper installation of the mechanical seal can compromise its effectiveness and lead to leakage. This can include incorrect alignment of the seal components, insufficient tightening of fasteners, or improper use of sealants or gaskets.
Seal Face Misalignment: If the seal faces are not properly aligned, they may not make adequate contact with each other, resulting in a poor seal. Misalignment can be caused by factors such as shaft deflection, bearing wear, or improper installation.
Excessive Shaft Movement: Excessive axial or radial movement of the pump shaft can cause mechanical seal leakage. This movement can be due to factors such as worn bearings, improper coupling alignment, or excessive vibration in the pump system.
Contaminants in the Pumped Fluid: Abrasive particles, chemicals, or solids present in the pumped fluid can damage the seal faces and compromise their ability to create an effective seal. This can lead to leakage over time.
Insufficient Lubrication or Cooling: Mechanical seals require proper lubrication and cooling to operate effectively. Inadequate lubrication or cooling can cause excessive friction, heat buildup, and accelerated wear of the seal components, resulting in leakage.
Seal Material Incompatibility: Using a mechanical seal made from incompatible materials for the pumped fluid can lead to seal degradation and leakage. It is important to select seal materials that are compatible with the characteristics of the fluid being pumped, including its temperature, pH, and chemical composition.
Operating Conditions: Extreme operating conditions, such as high temperatures, high pressures, or frequent starts and stops, can put additional stress on the mechanical seal and increase the risk of leakage.
Regular inspection, proper maintenance, and adherence to manufacturer guidelines for installation and operation can help minimize mechanical seal leakage in fire pumps. Additionally, using high-quality seals appropriate for the specific application and maintaining proper fluid cleanliness can also contribute to reducing seal leakage.
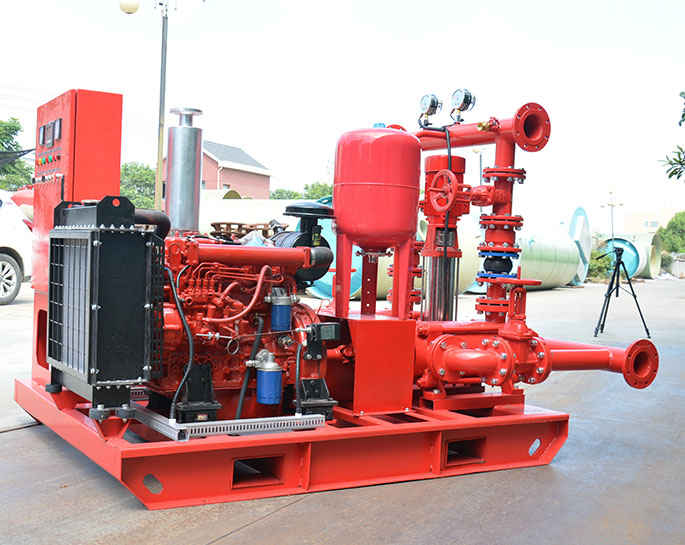