Can electric fire pump systems be equipped with condition monitoring and predictive maintenance capabilities to anticipate and prevent potential failures?
Apr 09, 2024
Share:
Yes, electric fire pump systems can indeed be equipped with condition monitoring and predictive maintenance capabilities to anticipate and prevent potential failures. Here's how:
1. **Vibration Monitoring**: Vibration monitoring sensors can be installed on motors, pumps, and other rotating machinery within the fire pump system. These sensors detect abnormal vibration patterns that may indicate bearing wear, misalignment, or other mechanical issues. By analyzing vibration data, maintenance personnel can identify potential problems early and schedule maintenance before a failure occurs.
2. **Temperature Monitoring**: Temperature sensors can be used to monitor the temperature of critical components such as motors, bearings, and electrical connections. Elevated temperatures can indicate issues such as overheating, insulation breakdown, or insufficient cooling. Early detection of temperature anomalies allows for timely intervention to prevent equipment damage or failure.
3. **Pressure and Flow Monitoring**: Monitoring pressure and flow rates within the fire pump system can provide insights into system performance and detect abnormalities such as leaks, blockages, or pump cavitation. Anomalies in pressure or flow can trigger alerts for maintenance personnel to investigate and address potential issues before they escalate.
4. **Remote Monitoring and Diagnostics**: Implementing remote monitoring capabilities allows for real-time monitoring of the fire pump system's performance from a central location. Remote diagnostics tools can analyze data collected from various sensors to identify trends, anomalies, or predictive indicators of impending failures. Maintenance personnel can receive alerts and diagnostic reports, enabling them to take proactive measures to prevent failures.
5. **Data Analytics and Predictive Algorithms**: Advanced data analytics techniques, including machine learning algorithms, can be employed to analyze historical data and identify patterns indicative of potential failures. By training predictive models on past maintenance records and performance data, the system can anticipate maintenance needs and predict the remaining useful life of critical components. This enables maintenance schedules to be optimized, reducing downtime and extending equipment lifespan.
6. **Integration with Maintenance Management Systems**: Integrating condition monitoring data with maintenance management systems allows for seamless scheduling of preventive maintenance activities based on real-time equipment condition. Work orders can be automatically generated for inspection, lubrication, alignment, or other maintenance tasks, ensuring that maintenance activities are carried out in a timely manner to prevent failures.
By integrating condition monitoring and predictive maintenance capabilities into electric fire pump systems, facility operators can proactively identify and address potential issues, enhance system reliability, and minimize the risk of equipment failure during critical fire protection scenarios.
1. **Vibration Monitoring**: Vibration monitoring sensors can be installed on motors, pumps, and other rotating machinery within the fire pump system. These sensors detect abnormal vibration patterns that may indicate bearing wear, misalignment, or other mechanical issues. By analyzing vibration data, maintenance personnel can identify potential problems early and schedule maintenance before a failure occurs.
2. **Temperature Monitoring**: Temperature sensors can be used to monitor the temperature of critical components such as motors, bearings, and electrical connections. Elevated temperatures can indicate issues such as overheating, insulation breakdown, or insufficient cooling. Early detection of temperature anomalies allows for timely intervention to prevent equipment damage or failure.
3. **Pressure and Flow Monitoring**: Monitoring pressure and flow rates within the fire pump system can provide insights into system performance and detect abnormalities such as leaks, blockages, or pump cavitation. Anomalies in pressure or flow can trigger alerts for maintenance personnel to investigate and address potential issues before they escalate.
4. **Remote Monitoring and Diagnostics**: Implementing remote monitoring capabilities allows for real-time monitoring of the fire pump system's performance from a central location. Remote diagnostics tools can analyze data collected from various sensors to identify trends, anomalies, or predictive indicators of impending failures. Maintenance personnel can receive alerts and diagnostic reports, enabling them to take proactive measures to prevent failures.
5. **Data Analytics and Predictive Algorithms**: Advanced data analytics techniques, including machine learning algorithms, can be employed to analyze historical data and identify patterns indicative of potential failures. By training predictive models on past maintenance records and performance data, the system can anticipate maintenance needs and predict the remaining useful life of critical components. This enables maintenance schedules to be optimized, reducing downtime and extending equipment lifespan.
6. **Integration with Maintenance Management Systems**: Integrating condition monitoring data with maintenance management systems allows for seamless scheduling of preventive maintenance activities based on real-time equipment condition. Work orders can be automatically generated for inspection, lubrication, alignment, or other maintenance tasks, ensuring that maintenance activities are carried out in a timely manner to prevent failures.
By integrating condition monitoring and predictive maintenance capabilities into electric fire pump systems, facility operators can proactively identify and address potential issues, enhance system reliability, and minimize the risk of equipment failure during critical fire protection scenarios.
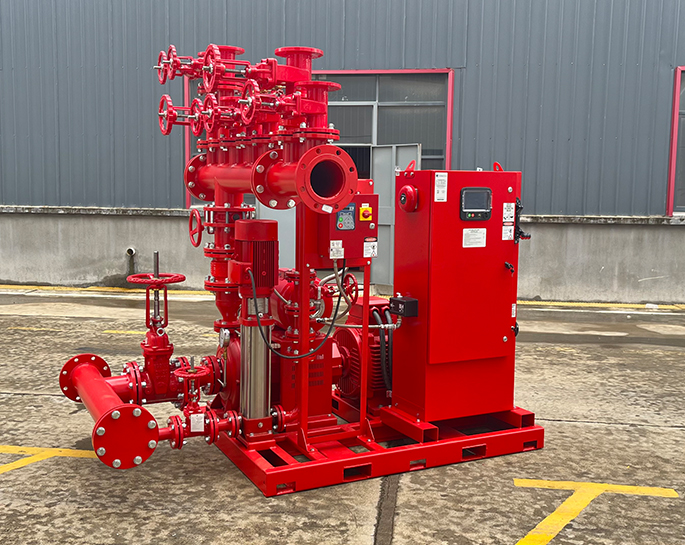