Are there specific requirements for fire pump installations in areas with corrosive atmospheres, such as near coastal regions?
Feb 01, 2024
Share:
Yes, installations of fire pumps in areas with corrosive atmospheres, such as near coastal regions where salt air can lead to corrosion, may require additional considerations and specific measures to ensure the reliability and longevity of the fire pump system. Here are some key considerations and requirements:
1. **Material Selection:**
- Choose materials that are resistant to corrosion. For example, stainless steel and corrosion-resistant alloys are often preferred for components exposed to salt air.
- The pump casing, impeller, motor housing, and other critical parts should be made of materials suitable for the corrosive environment.
2. **Coating and Protection:**
- Apply protective coatings or finishes to metal components to enhance their resistance to corrosion. This may include corrosion-resistant paints or coatings designed for marine environments.
- Consider using galvanized or coated fasteners to prevent corrosion.
3. **Enclosures and Housings:**
- Ensure that electrical components, control panels, and other vulnerable parts are housed in protective enclosures that are designed to resist corrosion.
- Enclosures should have appropriate ratings for the environment, such as NEMA 4X for outdoor use and resistance to corrosive agents.
4. **Regular Inspection and Maintenance:**
- Implement a more frequent inspection and maintenance schedule for fire pump systems in corrosive atmospheres. Regularly check for signs of corrosion, wear, or damage.
- Pay special attention to exposed electrical connections, wiring, and metal surfaces.
5. **Stainless Steel Piping:**
- Use corrosion-resistant materials for the piping system connected to the fire pump. Stainless steel or plastic piping can be suitable alternatives to traditional materials in corrosive environments.
6. **Ventilation and Air Circulation:**
- Design the pump room or pump enclosure with adequate ventilation to minimize the buildup of corrosive fumes.
- Ensure proper air circulation to prevent stagnant air pockets that can accelerate corrosion.
7. **Saltwater Intake Protection:**
- If the fire pump draws water from a saltwater source (such as for firefighting in coastal areas), install appropriate filtration and intake protection systems to prevent saltwater from damaging the pump.
8. **Compliance with Codes and Standards:**
- Ensure that the fire pump installation complies with relevant codes and standards that may have specific requirements for corrosive environments.
9. **Documentation and Recordkeeping:**
- Maintain detailed records of inspections, maintenance activities, and any corrective measures taken to address corrosion-related issues.
It's important to consult with local authorities, fire protection engineers, and follow applicable codes and standards (such as NFPA 20 for fire pump installations) to ensure that the fire pump system is designed and installed to withstand the corrosive conditions of the specific environment, such as coastal regions. Regular preventive measures and prompt corrective actions can help mitigate the impact of corrosion on fire pump systems in these challenging environments.
1. **Material Selection:**
- Choose materials that are resistant to corrosion. For example, stainless steel and corrosion-resistant alloys are often preferred for components exposed to salt air.
- The pump casing, impeller, motor housing, and other critical parts should be made of materials suitable for the corrosive environment.
2. **Coating and Protection:**
- Apply protective coatings or finishes to metal components to enhance their resistance to corrosion. This may include corrosion-resistant paints or coatings designed for marine environments.
- Consider using galvanized or coated fasteners to prevent corrosion.
3. **Enclosures and Housings:**
- Ensure that electrical components, control panels, and other vulnerable parts are housed in protective enclosures that are designed to resist corrosion.
- Enclosures should have appropriate ratings for the environment, such as NEMA 4X for outdoor use and resistance to corrosive agents.
4. **Regular Inspection and Maintenance:**
- Implement a more frequent inspection and maintenance schedule for fire pump systems in corrosive atmospheres. Regularly check for signs of corrosion, wear, or damage.
- Pay special attention to exposed electrical connections, wiring, and metal surfaces.
5. **Stainless Steel Piping:**
- Use corrosion-resistant materials for the piping system connected to the fire pump. Stainless steel or plastic piping can be suitable alternatives to traditional materials in corrosive environments.
6. **Ventilation and Air Circulation:**
- Design the pump room or pump enclosure with adequate ventilation to minimize the buildup of corrosive fumes.
- Ensure proper air circulation to prevent stagnant air pockets that can accelerate corrosion.
7. **Saltwater Intake Protection:**
- If the fire pump draws water from a saltwater source (such as for firefighting in coastal areas), install appropriate filtration and intake protection systems to prevent saltwater from damaging the pump.
8. **Compliance with Codes and Standards:**
- Ensure that the fire pump installation complies with relevant codes and standards that may have specific requirements for corrosive environments.
9. **Documentation and Recordkeeping:**
- Maintain detailed records of inspections, maintenance activities, and any corrective measures taken to address corrosion-related issues.
It's important to consult with local authorities, fire protection engineers, and follow applicable codes and standards (such as NFPA 20 for fire pump installations) to ensure that the fire pump system is designed and installed to withstand the corrosive conditions of the specific environment, such as coastal regions. Regular preventive measures and prompt corrective actions can help mitigate the impact of corrosion on fire pump systems in these challenging environments.
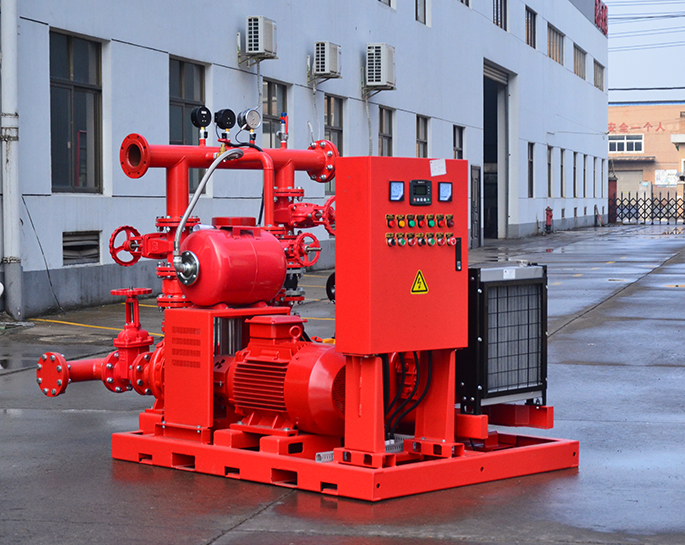