How to determine the part of the diesel engine pump set that leaks oil and achieve efficient use
Nov 17, 2022
Share:
Diesel fire pump sets sometimes have the appearance of oil leakage, so how do we go about analyzing the part of oil leakage, and then solve the problem, we introduce the following solutions for you.
1, The oil pressure is too high, also cause static joint surface oil leakage.
2, The purchase or homemade paper pad quality does not meet the requirements, such as thickness is not enough, or improper storage, wrinkled and deformed, or assembly does not pay attention to clean, dusty impurities, these are the causes of oil leakage.
3, Repair and maintenance operation technology is not good. At present, diesel engine pump sets are generally based on self-repair, because the level of repair technology can not keep up, self-repair often appear in this or that problem, especially when disassembling and assembling the machine does not pay attention to the method, the lack of special tools, so that the parts produce deformation, or even damage. Due to the deformation of parts, causing oil leakage. At present, the general disassembly method with the main bearing seat cover mounting bolts, screwed into the main bearing seat cover on the diagonal disassembly screw hole, top out the main bearing seat cover. It is difficult to synchronize the progress of the two bolts in the disassembly process, which is the main reason for the deformation of the main bearing cover.
4, Static joint surface quality itself, it is mainly determined by the precision of the processing equipment itself and storage and transportation conditions. If the equipment precision is high, static joint surface flatness, roughness can reach the drawing design requirements, and in the storage and transportation process to prevent bumping, etc., it is not difficult to achieve static joint surface completely sealed. However, due to the low level of precision and technology of some manufacturers' equipment, the storage and transportation conditions and management level cannot fully guarantee that there is no bumping and scratching.
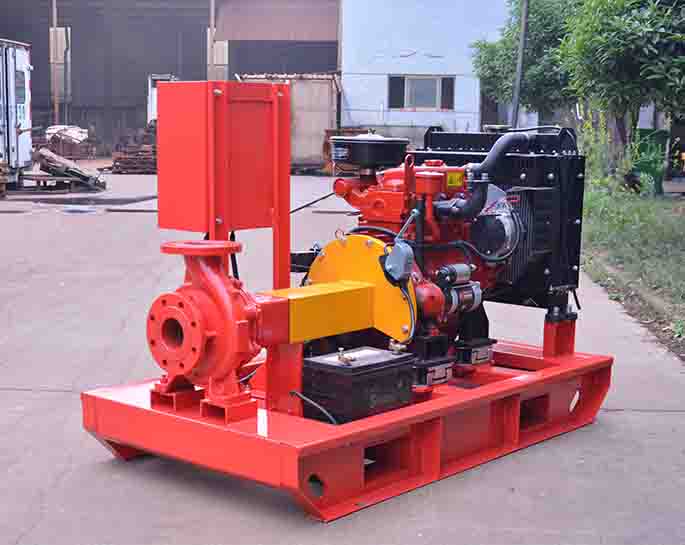
What measures are there to prevent this?
1, The disassembly process should take synchronous operation method, such as two people operating at the same time, try to achieve uniform screwing bolts.
2, The use of sealant adhesive, can play a sealing, leak-proof, tightening and blocking the role of the gap, to prevent leakage of oil purposes.
3、Pull-out device is used as far as possible in places with conditions in order to fundamentally solve the synchronization problem.
1, The oil pressure is too high, also cause static joint surface oil leakage.
2, The purchase or homemade paper pad quality does not meet the requirements, such as thickness is not enough, or improper storage, wrinkled and deformed, or assembly does not pay attention to clean, dusty impurities, these are the causes of oil leakage.
3, Repair and maintenance operation technology is not good. At present, diesel engine pump sets are generally based on self-repair, because the level of repair technology can not keep up, self-repair often appear in this or that problem, especially when disassembling and assembling the machine does not pay attention to the method, the lack of special tools, so that the parts produce deformation, or even damage. Due to the deformation of parts, causing oil leakage. At present, the general disassembly method with the main bearing seat cover mounting bolts, screwed into the main bearing seat cover on the diagonal disassembly screw hole, top out the main bearing seat cover. It is difficult to synchronize the progress of the two bolts in the disassembly process, which is the main reason for the deformation of the main bearing cover.
4, Static joint surface quality itself, it is mainly determined by the precision of the processing equipment itself and storage and transportation conditions. If the equipment precision is high, static joint surface flatness, roughness can reach the drawing design requirements, and in the storage and transportation process to prevent bumping, etc., it is not difficult to achieve static joint surface completely sealed. However, due to the low level of precision and technology of some manufacturers' equipment, the storage and transportation conditions and management level cannot fully guarantee that there is no bumping and scratching.
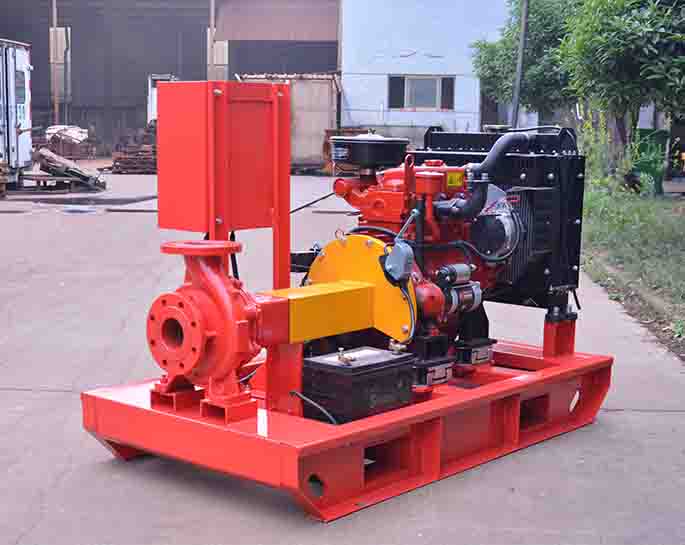
What measures are there to prevent this?
1, The disassembly process should take synchronous operation method, such as two people operating at the same time, try to achieve uniform screwing bolts.
2, The use of sealant adhesive, can play a sealing, leak-proof, tightening and blocking the role of the gap, to prevent leakage of oil purposes.
3、Pull-out device is used as far as possible in places with conditions in order to fundamentally solve the synchronization problem.